INDUSTRIAL
FABRICATION SERVICES

INDUSTRIAL
FABRICATION SERVICES

From Mission Accepted to Mission Accomplished.
The Industry Leader in Highly Engineered Specialty Industrial Solutions
Over 40 years of experience have earned Craftsmen Industries a solid reputation as the leading manufacturer of industrial solutions for global utilization.
Craftsmen serves government agencies, armed forces, corporations, and non-profit organizations that leverage static and mobile solutions for disaster relief response, military, aerospace, defense, medical services, power, water, training, and many other initiatives.
The Industry Leader in Highly Engineered Specialty Industrial Solutions
Over 40 years of experience has earned Craftsmen Industries a solid reputation as the leading manufacturer of industrial solutions for global utilization.
Craftsmen serves government agencies, armed forces, corporations, and non-profit organizations, who leverage static and mobile solutions for disaster relief response, military, aerospace, defense, medical services, power, water, training, and many other initiatives.
Our strength is built upon our end-to-end integration of the entire creative, design, engineering, fabrication, and graphics process. This allows us to take loosely defined ideas or ambiguous concepts and turn them into reality fast, without compromising concept, timeline, or quality. Because we own the entire highly-integrated production process, our product is reliable, high quality, on time, and on budget.
Craftsmen is the perfect partner to bring your concept to reality.
The Craftsmen Difference:
DESIGN - ENGINEERING - FABRICATION
GRAPHICS - PAINT - 3D
All Under One Roof!
The Industry Leader in Highly Engineered Specialty Industrial Solutions
Over 40 years of experience have earned Craftsmen Industries a solid reputation as the leading manufacturer of industrial solutions for global utilization.
Craftsmen serves government agencies, armed forces, corporations, and non-profit organizations that leverage static and mobile solutions for disaster relief response, military, aerospace, defense, medical services, power, water, training, and many other initiatives.
Our strength is built upon our end-to-end integration of the entire creative, design, engineering, fabrication, and graphics process. This allows us to take loosely defined ideas or ambiguous concepts and turn them into reality fast, without compromising concept, timeline, or quality. Because we own the entire highly-integrated production process, our product is reliable, high quality, on time, and on budget.
Craftsmen is the perfect partner to bring your concept to reality.
The Craftsmen Difference:
DESIGN - ENGINEERING – FABRICATION
GRAPHICS - PAINT – 3D
All Under One Roof!
Dedicated to the Highest Quality Standards
We prioritize superior quality management and are certified by ASR with the prestigious AS9100D and ISO 9001:2015 certifications.
Contact us to find out how Craftsmen
can turn your idea into a reality
or Call Today 800.373.3575
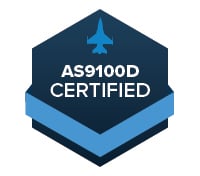
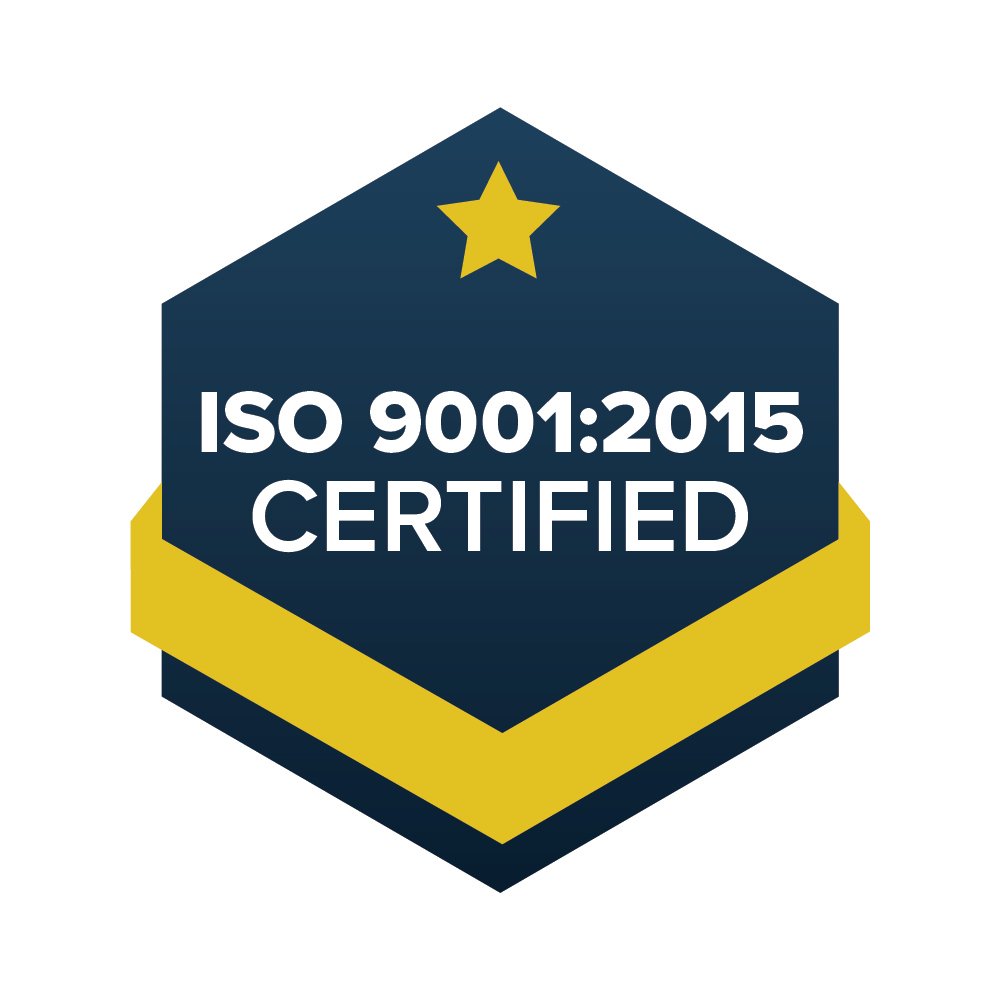
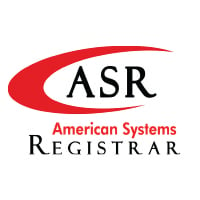
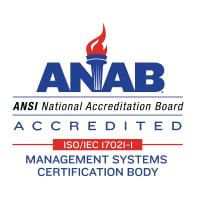
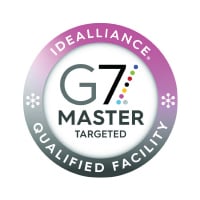
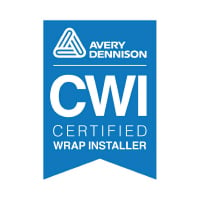
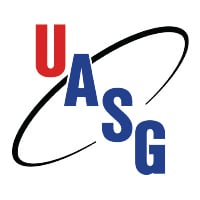
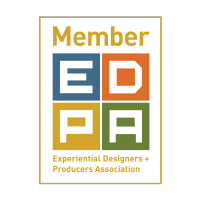

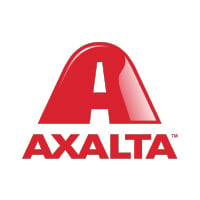
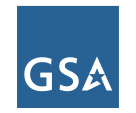
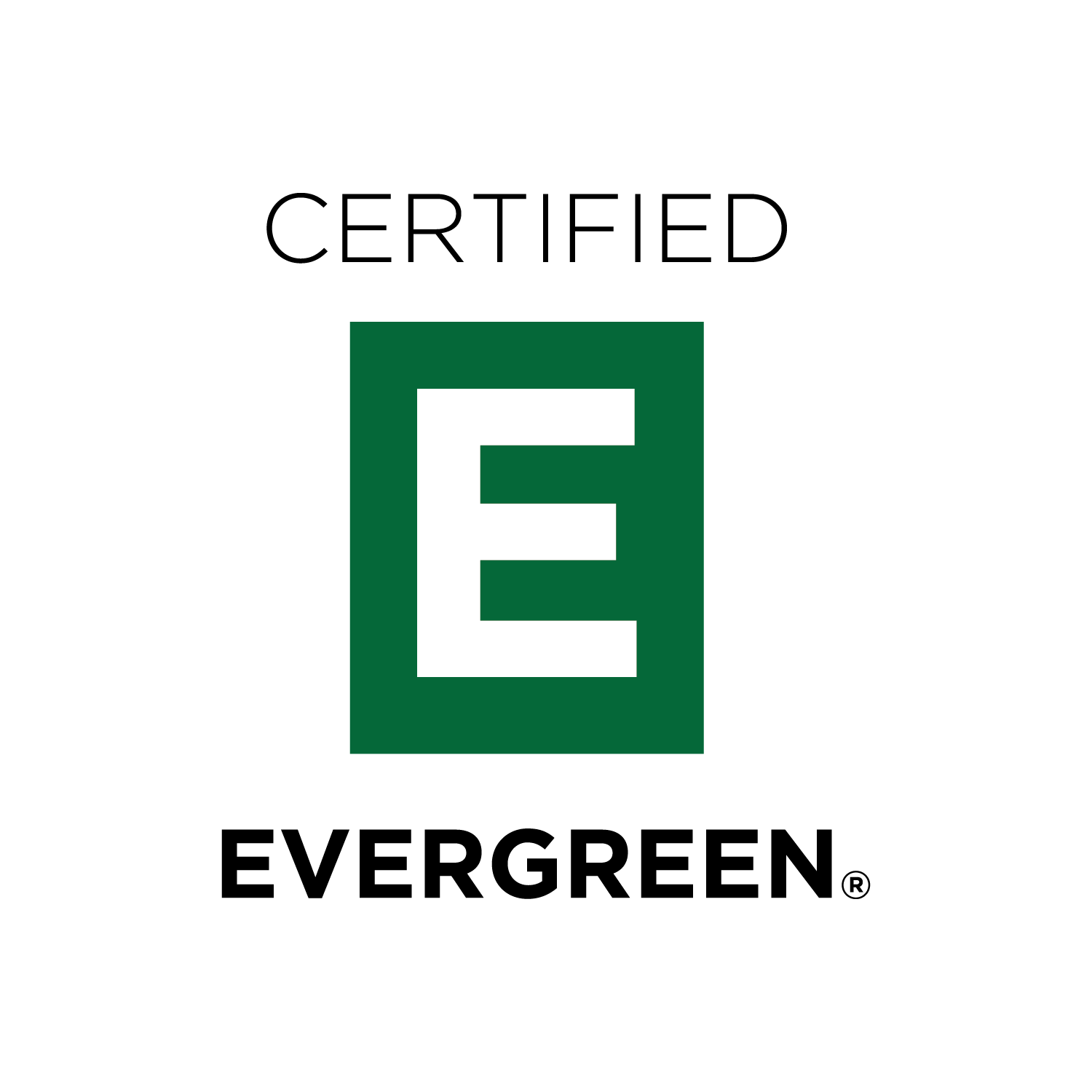
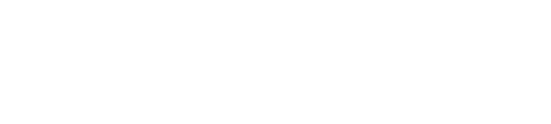
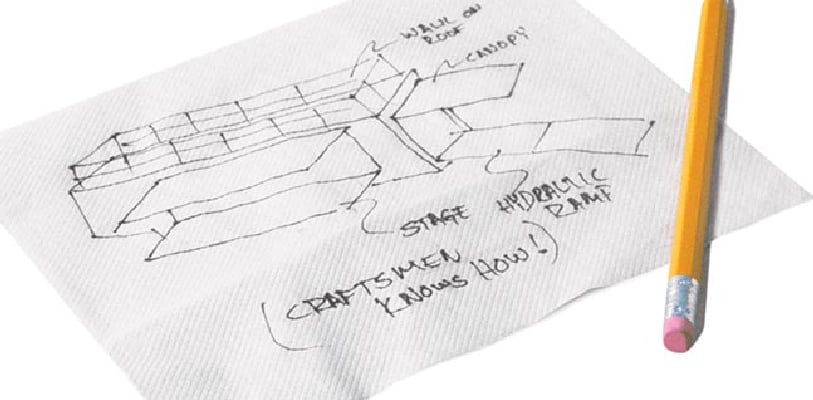
Vision
Tell us about your idea! Describe it, sketch it, or show us your designs.
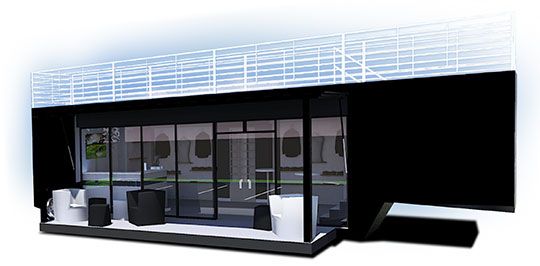
Design
We design your solution down to the last bolt.
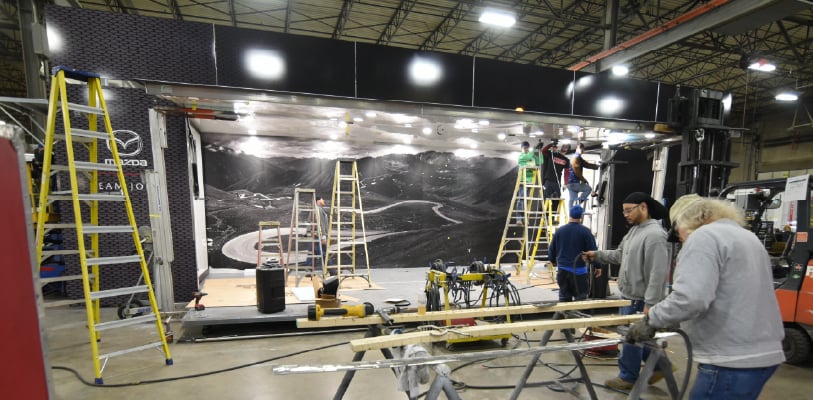
Build
We custom fabricate your build in-house.
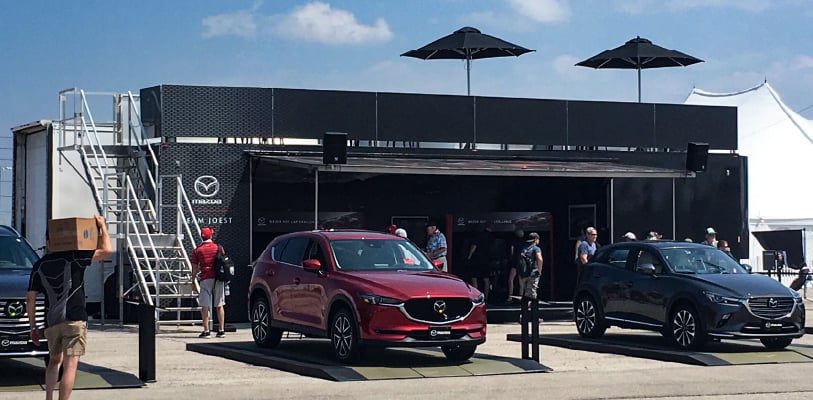
Deliver
We deliver your asset on time as promised.
Trusted by these VALUED CLIENTS
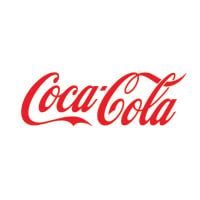
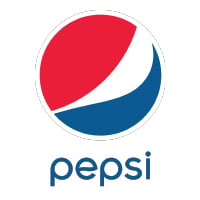
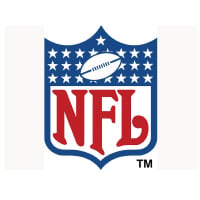
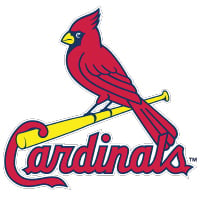
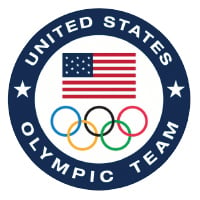
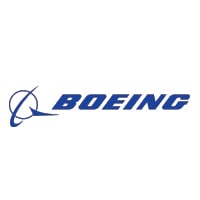
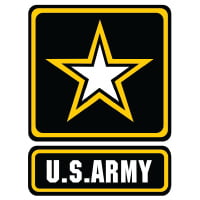
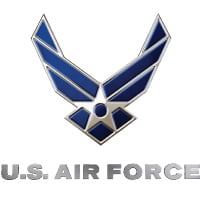
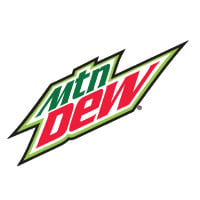
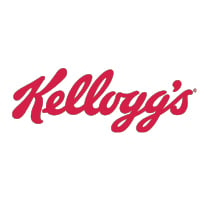
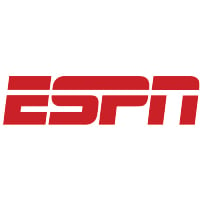
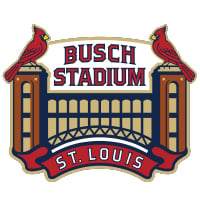
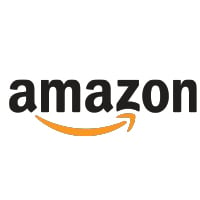
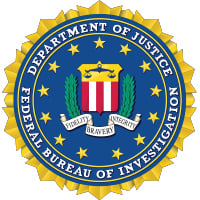
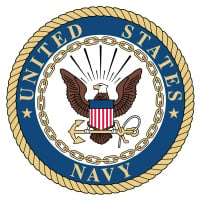
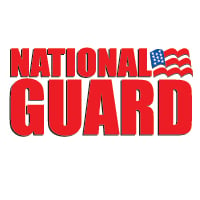
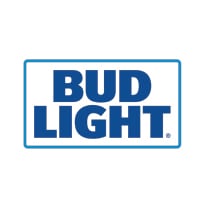
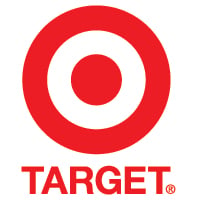
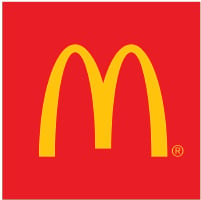
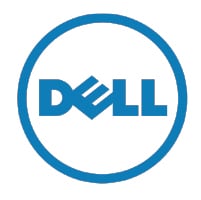
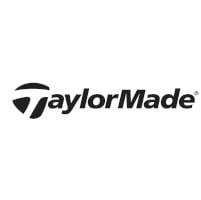

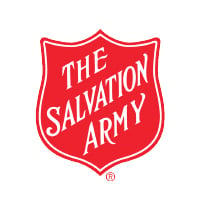
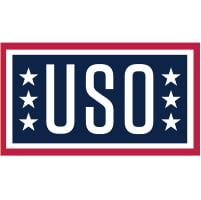
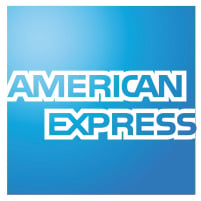
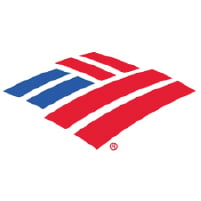
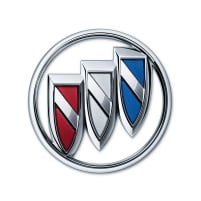
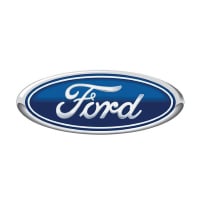
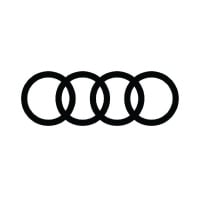
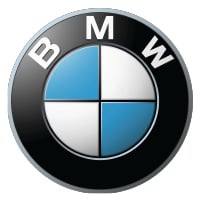
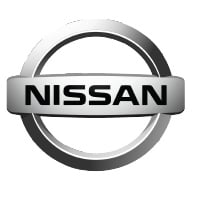
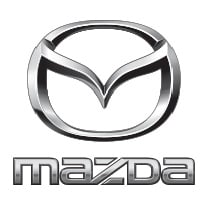
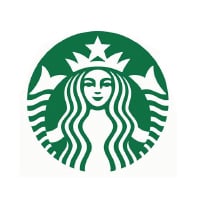
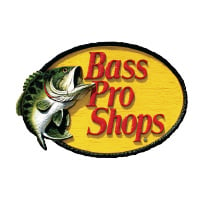
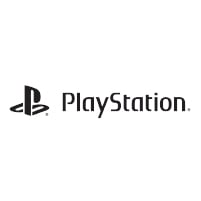
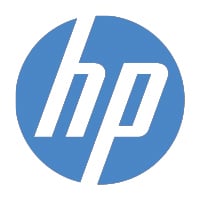
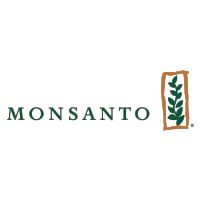
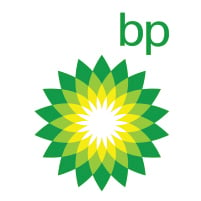
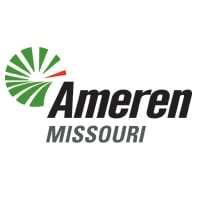
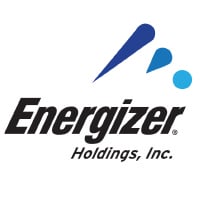
Contact Us
Our Work
Click the Area of Interest Below to See More
Precision Engineering for Custom-Built Solutions
Struggling to find a fabrication partner that delivers both precision and durability? Without expert craftsmanship, your projects may face delays, inefficiencies, or subpar results. At Craftsmen Industries, we provide high-quality industrial fabrication services tailored to your unique needs. With decades of experience, cutting-edge technology, and a team of skilled engineers, we bring your concepts to life with precision cutting, welding, forming, and assembly.
Whether you need custom metal fabrication, large-scale structural components, or turnkey manufacturing solutions, we guarantee superior craftsmanship, efficiency, and reliability. Contact us today to discuss your project and see how we can elevate your industrial fabrication needs!
Why Choose Craftsmen Industries
Expertise, Precision, and Unmatched Quality in Every Project
State-of-the-Art Fabrication Facility
With a 127,000 sq. ft. advanced manufacturing facility, we are equipped with the latest CNC machines, laser cutters, press brakes, robotic welders, and high-capacity forming tools to deliver superior fabrication with tight tolerances and consistent precision.
Custom Engineering & Turnkey Solutions
We specialize in custom-built solutions, offering concept-to-completion fabrication tailored to your exact specifications. Our expert engineering team collaborates with you to develop innovative designs that optimize functionality and performance.
Skilled Workforce & Certified Fabricators
Our team of highly trained fabricators, welders, and machinists ensures every project meets the highest industry standards. We hold certifications in AWS (American Welding Society), ASME (American Society of Mechanical Engineers), and other industry benchmarks, guaranteeing top-tier quality and compliance.
Precision Machining & Metal Forming
We leverage advanced machining capabilities to shape, cut, and assemble materials with extreme accuracy. Our automated press brakes and high-precision laser cutting technology allow us to fabricate complex components with superior strength and detail.
High-Quality Materials & Durability
We source top-grade metals, composites, and specialty materials to ensure the durability and longevity of every fabricated component. Our materials are engineered to withstand extreme environmental conditions, heavy loads, and continuous operation.
Scalability & Quick Turnaround
Whether you need a one-off prototype or high-volume production, our fabrication process is designed for scalability without compromising on quality. Our efficient workflow and lean manufacturing principles allow us to deliver projects on time and within budget.
Comprehensive Testing & Quality Assurance
Our rigorous inspection and testing processes, including structural integrity checks, stress testing, and precision measurements, ensure that every fabricated product meets or exceeds industry specifications.
Our Industrial Fabrication Process
Craftsmen Industries follows a streamlined, precision-driven approach to ensure high-quality industrial fabrication, from concept to completion.
- Consultation & Project Planning
We begin with a detailed consultation to understand your specifications, performance requirements, and industry regulations. Our team collaborates with you to develop a fabrication strategy that meets your exact needs. - Engineering & Design
Our in-house engineers create detailed CAD models and blueprints, ensuring structural integrity, efficiency, and compliance with industry standards. We optimize designs for durability and cost-effective manufacturing. - Material Selection & Preparation
We source premium-grade metals and industrial materials suited to your project’s environmental and operational demands. Materials are cut, shaped, and prepped using precision CNC machining and laser cutting technology. - Fabrication & Welding
Our certified welders and skilled fabricators assemble components with precision, using advanced welding, forming, and joining techniques to ensure strength, stability, and long-term performance. - Quality Control & Testing
Every fabricated structure undergoes rigorous inspections, non-destructive testing (NDT), and compliance verification to meet industry-specific regulations, safety standards, and customer requirements. - Finishing & Coatings
For enhanced durability, we apply protective coatings, corrosion-resistant finishes, and paint treatments as needed. This step ensures longevity and resilience in demanding environments. - Assembly & Integration
If required, our team integrates fabricated components into full systems, ensuring proper fit, alignment, and functionality before final delivery. - Delivery & Installation
We provide safe packaging, on-time delivery, and professional installation support, ensuring seamless integration into your operations.
Craftsmen Industries delivers precision-engineered industrial fabrication solutions that meet the toughest demands, ensuring quality, efficiency, and long-term performance.
What Other Services We Offer for Industrial Fabrication
At Craftsmen Industries, we go beyond traditional industrial fabrication to provide custom-engineered solutions for military, industrial, and commercial applications.
Military & Industrial Fabrication
We manufacture rugged, precision-engineered components for military, aerospace, and heavy industrial applications. Our fabrication process ensures exceptional durability, strength, and compliance with industry standards, making our products ideal for mission-critical environments.
Rapid Prototyping
With advanced CNC machining, laser cutting, and additive manufacturing, we provide fast, cost-effective prototype fabrication. Our rapid prototyping services enable businesses to test, refine, and develop custom metal components, enclosures, and structures with minimal lead time.
Maintenance Platforms
We design and fabricate custom maintenance platforms, workstations, and access structures to enhance efficiency and safety in industrial settings. Built with high load-bearing capacity and OSHA-compliant designs, our platforms provide safe and ergonomic access for heavy equipment maintenance and operations.
Mobile Water Filtration
For disaster relief, military operations, and remote industrial sites, we manufacture custom mobile water filtration units that provide on-the-go purification. Our systems are engineered for reliability and efficiency, ensuring access to clean, safe water in any environment.
Mobile Power Generation
We fabricate custom enclosures, generator housings, and mobile power stations to provide stable, on-demand energy for construction, disaster response, and remote operations. Our rugged, weather-resistant designs ensure durability in harsh conditions.
Wide Format Printing Services
Beyond fabrication, we offer high-quality wide format printing services for industrial, commercial, and promotional applications. Our state-of-the-art printing technology produces high-resolution, durable graphics for signage, trade shows, wall murals, fleet wraps, and more. We use weather-resistant materials to ensure long-lasting impact indoors and outdoors.
About Craftsmen
Decades of expertise, innovation, and precision.
With over 40 years of expertise, Craftsmen Industries specializes in precision industrial fabrication for military, industrial, and commercial applications. Operating from our 127,000 sq. ft. facility in St. Charles, Missouri, we handle everything in-house, from design and engineering to production.
Our team of skilled engineers and certified welders delivers high-performance solutions using advanced CNC machining, laser cutting, and welding. As a certified company, we ensure durability, precision, and compliance in every project, from mobile infrastructure to rapid prototyping.
At Craftsmen Industries, we don’t just fabricate—we engineer solutions that drive industries forward.
Industries We Serve
Craftsmen Industries provides precision-engineered industrial fabrication solutions across a wide range of industries, delivering durable and compliant structures for demanding applications.
Military & Defense
We fabricate rugged, mission-critical structures such as mobile command centers, maintenance platforms, and power generation units built to withstand extreme conditions.
Aerospace
Our high-precision fabrication services support ground support equipment, maintenance platforms, and aerospace infrastructure with strict compliance to industry standards.
Energy & Utilities
We manufacture mobile power generation units, water filtration systems, and structural components to support renewable energy, oil & gas, and utility infrastructure.
Manufacturing & Industrial
From custom machinery enclosures to heavy-duty platforms and workstations, we create durable fabrication solutions tailored to industrial operations.
Transportation & Logistics
We provide high-strength metal fabrication for fleet infrastructure, loading platforms, and mobile service units to enhance operational efficiency.
Construction & Infrastructure
Our fabricated components, including steel structures, modular enclosures, and mobile workstations, support large-scale construction and infrastructure projects.
Medical & Emergency Response
We fabricate mobile medical units, disaster relief structures, and emergency response equipment to aid healthcare and rescue operations.
Craftsmen Industries is a trusted partner across multiple industries, delivering custom, high-performance fabrication solutions built for reliability, safety, and long-term use.
Frequently Asked Questions
Can you handle custom fabrication projects?
Yes, we specialize in custom industrial fabrication, working closely with clients to design and manufacture tailored solutions that meet specific project requirements.
Do you offer prototyping before full production?
Absolutely. We provide rapid prototyping services, allowing clients to test and refine their designs before committing to full-scale production.
Do you provide installation and support after fabrication?
Yes, we offer full-service solutions, including delivery, installation, and ongoing support to ensure seamless integration and long-term performance of our fabricated products.
How do you ensure quality and compliance in your fabrication projects?
We follow strict quality control measures, utilize advanced fabrication technology, and adhere to industry-specific standards to ensure precision, durability, and compliance with regulatory requirements.
What is the typical lead time for an industrial fabrication project?
Lead times vary based on project complexity, material availability, and production scale. However, we prioritize efficiency and offer expedited services when needed to meet critical deadlines.
Bring Your Vision to Life with Precision Industrial Fabrication
Looking for durable, high-performance fabrication solutions? At Craftsmen Industries, we turn complex ideas into reality with expert engineering, advanced manufacturing, and high-quality materials. Whether you need custom structures, mobile solutions, or heavy-duty industrial components, our team ensures precision, efficiency, and reliability every step of the way. Discuss your project with us and experience fabrication solutions built to perform in the toughest environments.